Технологија сечења плочица, као кључни корак у процесу производње полупроводника, директно је повезана са перформансама чипа, приносом и трошковима производње.
#01 Позадина и значај сецкања вафла
1.1 Дефиниција сечења вафла
Сечење плочица (такође познато као скрайбовање) је суштински корак у производњи полупроводника, чији је циљ подела обрађених плочица на више појединачних чипова. Ови чипови обично садрже комплетну функционалност кола и представљају основне компоненте које се на крају користе у производњи електронских уређаја. Како дизајн чипова постаје сложенији, а димензије се настављају смањивати, захтеви за прецизност и ефикасност технологије сечења плочица постају све строжи.
У практичним операцијама, сечење вафла обично користи високопрецизне алате као што су дијамантска сечива како би се осигурало да сваки штап остане нетакнут и потпуно функционалан. Кључни кораци укључују припрему пре сечења, прецизну контролу током процеса сечења и контролу квалитета након сечења.
Пре сечења, плочица мора бити обележена и позиционирана како би се осигурале прецизне путање сечења. Током сечења, параметри као што су притисак алата и брзина морају бити строго контролисани како би се спречило оштећење плочице. Након сечења, спроводе се свеобухватне инспекције квалитета како би се осигурало да сваки чип испуњава стандарде перформанси.
Основни принципи технологије сечења плочица обухватају не само избор опреме за сечење и подешавање параметара процеса, већ и утицај механичких својстава и карактеристика материјала на квалитет сечења. На пример, силицијумске плочице са ниском диелектричном вредношћу (low-k), због својих лошијих механичких својстава, веома су подложне концентрацији напона током сечења, што доводи до кварова као што су крзање и пуцање. Ниска тврдоћа и кртост материјала са ниском диелектричном вредношћу чине их склонијим структурним оштећењима под механичком силом или термичким напрезањем, посебно током сечења. Контакт између алата и површине плочице, заједно са високим температурама, може додатно погоршати концентрацију напона.
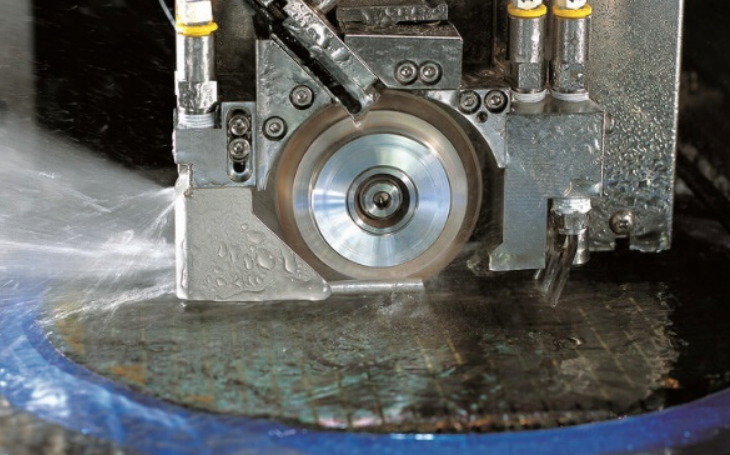
Са напретком у науци о материјалима, технологија сечења плочица се проширила изван традиционалних полупроводника на бази силицијума и обухватила нове материјале попут галијум нитрида (GaN). Ови нови материјали, због своје тврдоће и структурних својстава, представљају нове изазове за процесе сечења, захтевајући даља побољшања алата и техника сечења.
Као критични процес у полупроводничкој индустрији, сечење плочица се наставља оптимизовати као одговор на стално растуће захтеве и технолошки напредак, постављајући темеље за будућу микроелектронику и технологије интегрисаних кола.
Побољшања у технологији сечења плочица иду даље од развоја помоћних материјала и алата. Она такође обухватају оптимизацију процеса, побољшања перформанси опреме и прецизну контролу параметара сечења. Ова побољшања имају за циљ да обезбеде високу прецизност, ефикасност и стабилност у процесу сечења плочица, задовољавајући потребе полупроводничке индустрије за мањим димензијама, већом интеграцијом и сложенијим структурама чипова.
Подручје побољшања | Конкретне мере | Ефекти |
Оптимизација процеса | - Побољшати почетне припреме, као што су прецизније позиционирање плочице и планирање путање. | - Смањите грешке сечења и побољшајте стабилност. |
- Минимизирајте грешке при сечењу и побољшајте стабилност. | - Усвојите механизме за праћење и повратне информације у реалном времену како бисте подесили притисак, брзину и температуру алата. | |
- Смањује стопу ломљења плочице и побољшава квалитет чипа. | ||
Побољшање перформанси опреме | - Користите високопрецизне механичке системе и напредну технологију аутоматизације. | - Повећајте тачност сечења и смањите расипање материјала. |
- Увести технологију ласерског сечења погодну за плочице од материјала високе тврдоће. | - Побољшајте ефикасност производње и смањите ручне грешке. | |
- Повећати аутоматизацију опреме за аутоматско праћење и подешавања. | ||
Прецизна контрола параметара | - Фино подесите параметре као што су дубина резања, брзина, тип алата и методе хлађења. | - Обезбедите интегритет чипа и електричне перформансе. |
- Прилагодите параметре на основу материјала, дебљине и структуре плочице. | - Повећајте принос, смањите отпад материјала и смањите трошкове производње. | |
Стратешки значај | - Континуирано истраживати нове технолошке путеве, оптимизовати процесе и унапређивати могућности опреме како би се задовољиле потребе тржишта. | - Побољшати принос и перформансе производње чипова, подржавајући развој нових материјала и напредних дизајна чипова. |
1.2 Значај сецкања вафла
Сечење плочица игра кључну улогу у процесу производње полупроводника, директно утичући на наредне кораке, као и на квалитет и перформансе финалног производа. Његов значај се може детаљно описати на следећи начин:
Прво, тачност и доследност сечења су кључни за обезбеђивање приноса и поузданости чипа. Током производње, плочице пролазе кроз више корака обраде како би се формирале бројне сложене структуре кола, које морају бити прецизно подељене на појединачне чипове (матрице). Ако постоје значајне грешке у поравнању или сечењу током процеса сечења, кола могу бити оштећена, што утиче на функционалност и поузданост чипа. Стога, технологија високопрецизног сечења не само да осигурава интегритет сваког чипа, већ и спречава оштећење унутрашњих кола, побољшавајући укупну стопу приноса.
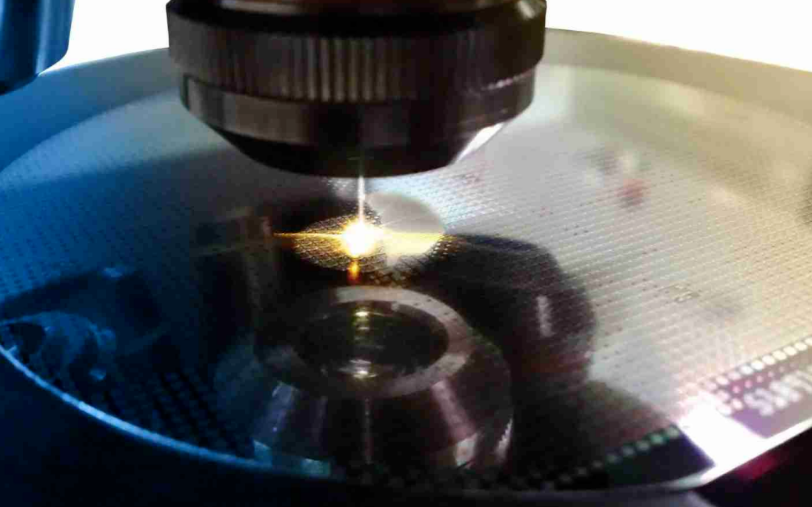
Друго, сецкање вафла има значајан утицај на ефикасност производње и контролу трошкова. Као кључни корак у производном процесу, његова ефикасност директно утиче на напредак наредних корака. Оптимизацијом процеса сецкања, повећањем нивоа аутоматизације и побољшањем брзине сечења, укупна ефикасност производње може се значајно побољшати.
С друге стране, расипање материјала током сечења је кључни фактор у управљању трошковима. Коришћење напредних технологија сечења не само да смањује непотребне губитке материјала током процеса сечења, већ и повећава искоришћење плочице, чиме се смањују трошкови производње.
Са напретком у технологији полупроводника, пречници плочица настављају да се повећавају, а густине кола се сходно томе повећавају, што поставља веће захтеве на технологију сечења. Веће плочице захтевају прецизнију контролу путања сечења, посебно у областима са великом густином кола, где чак и мала одступања могу довести до неисправности више чипова. Поред тога, веће плочице укључују више линија сечења и сложеније кораке процеса, што захтева даља побољшања прецизности, конзистентности и ефикасности технологија сечења како би се одговорило на ове изазове.
1.3 Процес сечења вафла
Процес сецкања вафла обухвата све кораке, од фазе припреме до коначне контроле квалитета, при чему је свака фаза кључна за обезбеђивање квалитета и перформанси сецканих чипова. У наставку је детаљно објашњење сваке фазе.
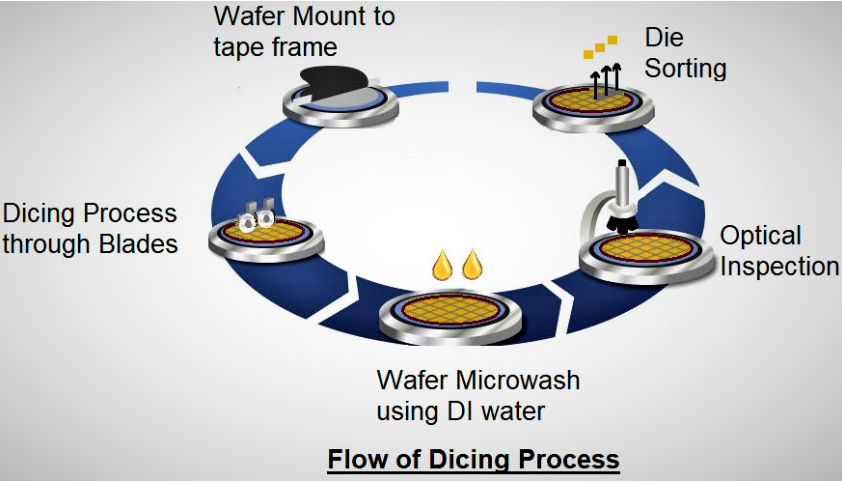
Фаза | Детаљан опис |
Припремна фаза | -Чишћење вафлаКористите воду високе чистоће и специјализована средства за чишћење, у комбинацији са ултразвучним или механичким рибањем, да бисте уклонили нечистоће, честице и загађиваче, осигуравајући чисту површину. -Прецизно позиционирањеКористите високопрецизну опрему како бисте осигурали да је плочица прецизно подељена дуж пројектованих путања сечења. -Фиксирање вафлеПричврстите плочицу на оквир траке како бисте одржали стабилност током сечења, спречавајући оштећења од вибрација или померања. |
Фаза сечења | -Сечење сечиваКористите ротирајуће сечива са дијамантским премазом велике брзине за физичко сечење, погодна за материјале на бази силицијума и исплатива. -Ласерско сечење коцкицаКористите високоенергетске ласерске зраке за бесконтактно сечење, идеално за крхке или материјале високе тврдоће попут галијум нитрида, нудећи већу прецизност и мањи губитак материјала. -Нове технологијеУвести технологије ласерског и плазма сечења како би се додатно побољшала ефикасност и прецизност, уз минимизирање зона погођених топлотом. |
Фаза чишћења | - Користите дејонизовану воду (ДЕ воду) и специјализована средства за чишћење, у комбинацији са ултразвучним или распршивачким чишћењем, да бисте уклонили остатке и прашину насталу током сечења, спречавајући да остаци утичу на наредне процесе или електричне перформансе чипа. - Деионизована вода високе чистоће спречава уношење нових загађивача, обезбеђујући чисто окружење за плочице. |
Фаза инспекције | -Оптичка инспекцијаКористите оптичке системе за детекцију у комбинацији са вештачком интелигенцијом (AI) алгоритмима за брзу идентификацију недостатака, осигуравајући да нема пукотина или крзања у сецканим комадићима, побољшавајући ефикасност инспекције и смањујући људске грешке. -Мерење димензијаПроверите да ли димензије чипа испуњавају спецификације дизајна. -Тестирање електричних перформансиОсигурати да електричне перформансе критичних чипова испуњавају стандарде, гарантујући поузданост у каснијим применама. |
Фаза сортирања | - Користите роботске руке или вакуумске чаше за одвајање квалификованих чипова од оквира траке и аутоматски их сортирајте на основу перформанси, обезбеђујући ефикасност производње и флексибилност уз истовремено побољшање прецизности. |
Процес сечења плочица обухвата чишћење плочица, позиционирање, сечење, чишћење, инспекцију и сортирање, при чему је сваки корак критичан. Са напретком у аутоматизацији, ласерском сечењу и технологијама инспекције помоћу вештачке интелигенције, модерни системи за сечење плочица могу постићи већу прецизност, брзину и мањи губитак материјала. У будућности, нове технологије сечења попут ласера и плазме постепено ће заменити традиционално сечење сечивима како би задовољиле потребе све сложенијих дизајна чипова, додатно подстичући развој процеса производње полупроводника.
Технологија сечења плочица и њени принципи
Слика илуструје три уобичајене технологије сечења плочица:Сечење сечива,Ласерско сечење коцкицаиПлазма сецкањеУ наставку је детаљна анализа и додатно објашњење ове три технике:
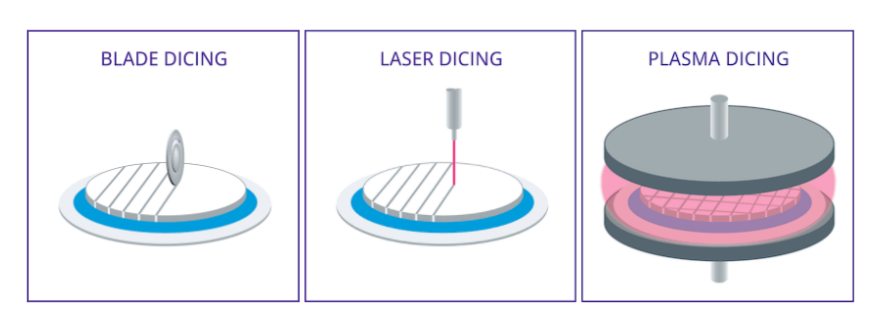
У производњи полупроводника, сечење плочица је кључни корак који захтева избор одговарајуће методе сечења на основу дебљине плочице. Први корак је одређивање дебљине плочице. Ако дебљина плочице прелази 100 микрона, као метод сечења може се изабрати сечење сечивом. Ако сечење сечивом није погодно, може се користити метод сечења са ломљењем, који укључује и технике сечења са цртањем и сечења сечивом.
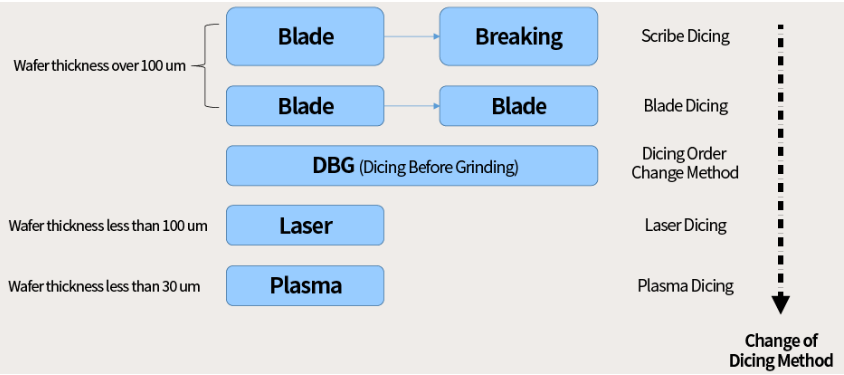
Када је дебљина плочице између 30 и 100 микрона, препоручује се DBG (Dice Before Grinding) метода. У овом случају, за постизање најбољих резултата може се изабрати сечење цртањем, сечење сечивом или подешавање редоследа сечења по потреби.
За ултратанке плочице дебљине мање од 30 микрона, ласерско сечење постаје преферирана метода због своје способности да прецизно сече танке плочице без наношења прекомерних оштећења. Ако ласерско сечење не може да задовољи специфичне захтеве, плазма сечење се може користити као алтернатива. Овај дијаграм тока пружа јасан пут доношења одлука како би се осигурало да се изабере најприкладнија технологија сечења плочица под различитим условима дебљине.
2.1 Технологија механичког сечења
Технологија механичког сечења је традиционална метода сечења вафла. Основни принцип је коришћење дијамантског брусног точка који се брзо ротира као алата за сечење вафла. Кључна опрема укључује ваздушно лежајево вретено, које покреће дијамантски брусни точак великим брзинама како би се извршило прецизно сечење или жлебљење дуж унапред дефинисане путање сечења. Ова технологија се широко користи у индустрији због ниске цене, високе ефикасности и широке применљивости.
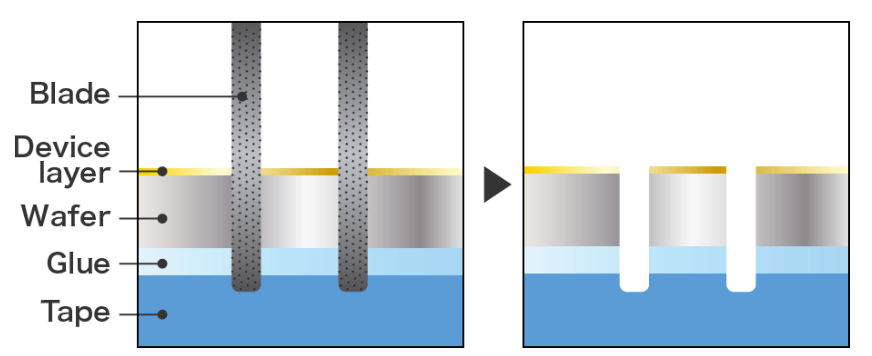
Предности
Висока тврдоћа и отпорност на хабање дијамантских брусних алата омогућавају да се технологија механичког сечења прилагоди потребама сечења различитих материјала за плочице, било да су то традиционални материјали на бази силицијума или новији сложени полупроводници. Његов рад је једноставан, са релативно ниским техничким захтевима, што додатно доприноси његовој популарности у масовној производњи. Поред тога, у поређењу са другим методама сечења попут ласерског сечења, механичко сечење има контролисаније трошкове, што га чини погодним за потребе производње великих количина.
Ограничења
Упркос бројним предностима, технологија механичког сечења такође има ограничења. Прво, због физичког контакта између алата и плочице, прецизност сечења је релативно ограничена, што често доводи до димензионалних одступања која могу утицати на тачност накнадног паковања и тестирања чипова. Друго, дефекти попут крзања и пукотина могу се лако појавити током процеса механичког сечења, што не само да утиче на стопу приноса, већ може негативно утицати и на поузданост и век трајања чипова. Оштећења изазвана механичким напрезањем су посебно штетна за производњу чипова високе густине, посебно при сечењу крхких материјала, где су ови проблеми израженији.
Технолошка побољшања
Да би превазишли ова ограничења, истраживачи континуирано оптимизују процес механичког сечења. Кључна побољшања укључују унапређење дизајна и избора материјала брусних точкова како би се побољшала прецизност сечења и издржљивост. Поред тога, оптимизација структурног дизајна и система управљања опремом за сечење додатно је побољшала стабилност и аутоматизацију процеса сечења. Ова побољшања смањују грешке изазване људским операцијама и побољшавају конзистентност резова. Увођење напредних технологија инспекције и контроле квалитета за праћење аномалија у реалном времену током процеса сечења такође је значајно побољшало поузданост сечења и принос.
Будући развој и нове технологије
Иако технологија механичког сечења и даље заузима значајну позицију у сечењу плочица, нове технологије сечења брзо напредују како се процеси производње полупроводника развијају. На пример, примена технологије термичког ласерског сечења пружа нова решења за проблеме прецизности и дефеката у механичком резању. Ова метода бесконтактног сечења смањује физички напон на плочици, значајно смањујући учесталост крзања и пуцања, посебно при сечењу крхкијих материјала. У будућности, интеграција технологије механичког сечења са новим техникама сечења пружиће производњи полупроводника више опција и флексибилности, додатно побољшавајући ефикасност производње и квалитет чипа.
Закључно, иако технологија механичког резања има одређене недостатке, континуирана технолошка побољшања и њена интеграција са новим техникама резања омогућавају јој да и даље игра важну улогу у производњи полупроводника и одржи своју конкурентност у будућим процесима.
2.2 Технологија ласерског сечења
Технологија ласерског сечења, као нова метода у сечењу плочица, постепено је стекла широку пажњу у полупроводничкој индустрији због своје високе прецизности, одсуства механичких оштећења контакта и могућности брзог сечења. Ова технологија користи високу густину енергије и способност фокусирања ласерског зрака да би створила малу зону под утицајем топлоте на површини материјала плочице. Када се ласерски зрак примени на плочицу, генерисани термички напон узрокује ломљење материјала на одређеном месту, постижући прецизно сечење.
Предности технологије ласерског сечења
• Висока прецизностПрецизна могућност позиционирања ласерског зрака омогућава прецизност сечења на микронском или чак нанометарском нивоу, испуњавајући захтеве модерне производње интегрисаних кола високе прецизности и високе густине.
• Без механичког контактаЛасерско сечење избегава физички контакт са плочицом, спречавајући уобичајене проблеме код механичког сечења, као што су крзање и пуцање, значајно побољшавајући стопу приноса и поузданост чипова.
• Велика брзина сечењаВелика брзина ласерског сечења доприноси повећаној ефикасности производње, што га чини посебно погодним за сценарије велике брзине производње великих размера.
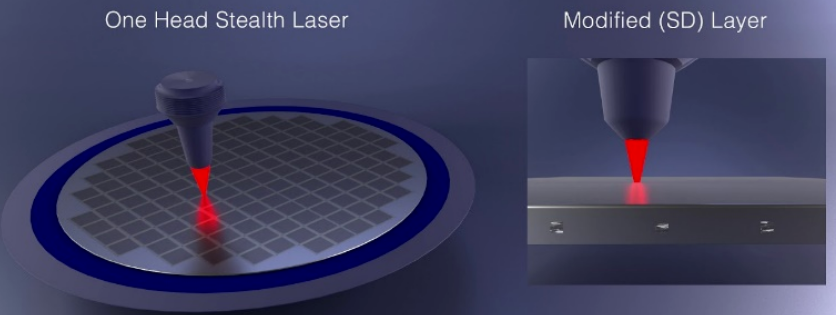
Суочени изазови
• Висока цена опремеПочетна инвестиција за опрему за ласерско сечење је висока, што представља економски притисак, посебно за мала и средња производна предузећа.
• Комплексна контрола процесаЛасерско сечење захтева прецизну контролу неколико параметара, укључујући густину енергије, положај фокуса и брзину сечења, што процес чини сложеним.
• Проблеми са зонама погођеним топлотомИако бесконтактна природа ласерског сечења смањује механичка оштећења, термички стрес изазван зоном утицаја топлоте (ЗТТ) може негативно утицати на својства материјала плочице. Потребна је даља оптимизација процеса како би се овај ефекат свео на минимум.
Правци технолошког унапређења
Да би се решили ови изазови, истраживачи се фокусирају на смањење трошкова опреме, побољшање ефикасности сечења и оптимизацију тока процеса.
• Ефикасни ласери и оптички системиРазвојем ефикаснијих ласера и напредних оптичких система могуће је смањити трошкове опреме, а истовремено побољшати прецизност и брзину сечења.
• Оптимизација параметара процесаСпроводе се детаљна истраживања интеракције између ласера и материјала за плочице како би се побољшали процеси који смањују зону утицаја топлоте, чиме се побољшава квалитет сечења.
• Интелигентни системи управљањаРазвој интелигентних технологија управљања има за циљ аутоматизацију и оптимизацију процеса ласерског сечења, побољшавајући његову стабилност и конзистентност.
Технологија ласерског сечења је посебно ефикасна у ултратанким плочицама и сценаријима високопрецизног сечења. Како се величине плочица повећавају, а густине кола расту, традиционалне методе механичког сечења се боре да задовоље захтеве модерне производње полупроводника за високом прецизношћу и високом ефикасношћу. Због својих јединствених предности, ласерско сечење постаје преферирано решење у овим областима.
Иако се технологија ласерског сечења и даље суочава са изазовима као што су високи трошкови опреме и сложеност процеса, њене јединствене предности у високој прецизности и бесконтактном оштећењу чине је важним правцем развоја у производњи полупроводника. Како ласерска технологија и интелигентни системи управљања настављају да напредују, очекује се да ће ласерско сечење додатно побољшати ефикасност и квалитет сечења плочица, покрећући континуирани развој индустрије полупроводника.
2.3 Технологија плазма сечења
Технологија плазма сечења, као нова метода сечења плочица, последњих година је добила значајну пажњу. Ова технологија користи високоенергетске плазма зраке за прецизно сечење плочица контролишући енергију, брзину и путању сечења плазма зрака, постижући оптималне резултате сечења.
Принцип рада и предности
Процес плазма сечења ослања се на плазма сноп високе температуре и енергије који генерише опрема. Овај сноп може загрејати материјал плочице до тачке топљења или испаравања за веома кратко време, што омогућава брзо сечење. У поређењу са традиционалним механичким или ласерским сечењем, плазма сечење је брже и ствара мању зону утицаја топлоте, ефикасно смањујући појаву пукотина и оштећења током сечења.
У практичним применама, технологија плазма сечења је посебно вешта у руковању плочицама сложених облика. Њен високоенергетски, подесиви плазма сноп може лако да сече плочице неправилног облика са великом прецизношћу. Стога, у производњи микроелектронике, посебно у прилагођеној и малосеријској производњи врхунских чипова, ова технологија показује велики потенцијал за широку употребу.
Изазови и ограничења
Упркос многим предностима технологије плазма сечења, она се суочава и са неким изазовима.
• Сложен процесПроцес плазма сечења је сложен и захтева високопрецизну опрему и искусне оператере како би се осигуралопрецизност и стабилност при резању.
• Контрола животне средине и безбедностВисокотемпературна и високоенергетска природа плазма снопа захтева строге мере контроле животне средине и безбедности, што повећава сложеност и трошкове имплементације.
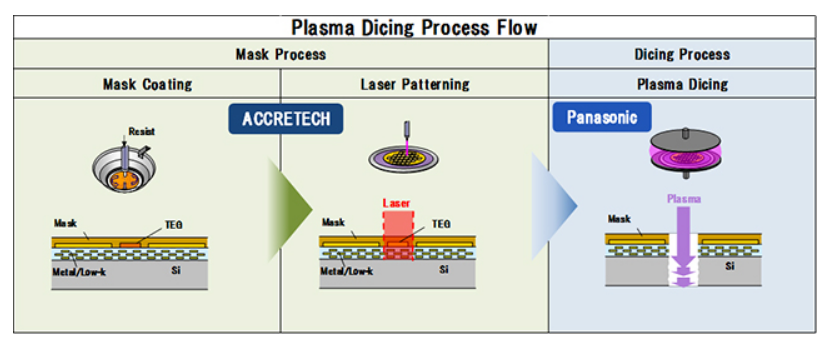
Будући правци развоја
Са технолошким напретком, очекује се да ће се изазови повезани са плазма резањем постепено превазићи. Развојем паметније и стабилније опреме за сечење, може се смањити зависност од ручних операција, чиме се побољшава ефикасност производње. Истовремено, оптимизација параметара процеса и окружења за сечење помоћи ће у смањењу безбедносних ризика и оперативних трошкова.
У полупроводничкој индустрији, иновације у технологији сечења и коцкицања плочица су кључне за покретање развоја индустрије. Технологија плазма сечења, са својом високом прецизношћу, ефикасношћу и способношћу да обрађује сложене облике плочица, појавила се као значајан нови играч у овој области. Иако неки изазови остају, ови проблеми ће се постепено решавати континуираним технолошким иновацијама, доносећи више могућности и прилика производњи полупроводника.
Перспективе примене технологије плазма сечења су огромне и очекује се да ће у будућности играти важнију улогу у производњи полупроводника. Кроз континуиране технолошке иновације и оптимизацију, плазма сечење не само да ће решити постојеће изазове, већ ће постати и снажан покретач раста полупроводничке индустрије.
2.4 Квалитет резања и фактори утицаја
Квалитет сечења плочица је кључан за накнадно паковање чипова, тестирање и укупне перформансе и поузданост финалног производа. Уобичајени проблеми који се јављају током сечења укључују пукотине, крзање и одступања у сечењу. На ове проблеме утиче неколико фактора који делују заједно.
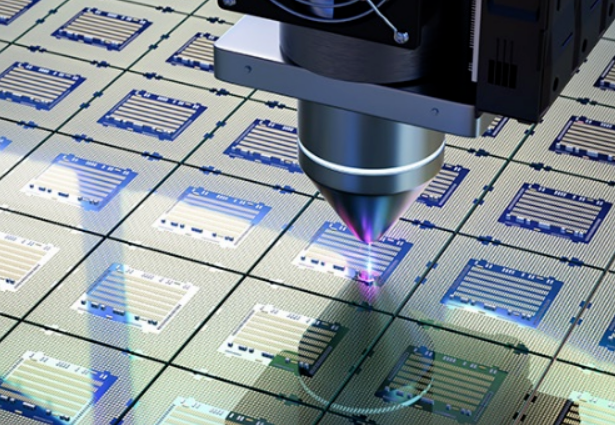
Категорија | Садржај | Утицај |
Параметри процеса | Брзина резања, брзина помака и дубина резања директно утичу на стабилност и прецизност процеса резања. Неправилна подешавања могу довести до концентрације напона и прекомерне зоне утицаја топлоте, што резултира пукотинама и крзањем. Подешавање параметара на основу материјала плочице, дебљине и захтева сечења је кључно за постизање жељених резултата резања. | Прави параметри процеса обезбеђују прецизно сечење и смањују ризик од дефеката попут пукотина и крзања. |
Фактори опреме и материјала | -Квалитет сечиваМатеријал, тврдоћа и отпорност на хабање сечива утичу на глаткоћу процеса сечења и равност површине реза. Сечива лошег квалитета повећавају трење и термички стрес, што потенцијално доводи до пукотина или крзања. Избор правог материјала сечива је кључан. -Перформансе расхладне течностиРасхладна средства помажу у смањењу температуре резања, минимизирању трења и уклањању остатака. Неефикасна расхладна течност може довести до високих температура и накупљања остатака, што утиче на квалитет и ефикасност резања. Избор ефикасних и еколошки прихватљивих расхладних средстава је од виталног значаја. | Квалитет сечива утиче на прецизност и глаткоћу реза. Неефикасно расхладно средство може довести до лошег квалитета и ефикасности сечења, што истиче потребу за оптималном употребом расхладног средства. |
Контрола процеса и инспекција квалитета | -Контрола процесаПраћење и подешавање кључних параметара сечења у реалном времену ради обезбеђивања стабилности и конзистентности у процесу сечења. -Инспекција квалитетаПровере изгледа након сечења, мерења димензија и испитивање електричних перформанси помажу у брзом идентификовању и решавању проблема са квалитетом, побољшавајући тачност и конзистентност сечења. | Правилна контрола процеса и инспекција квалитета помажу у обезбеђивању конзистентних, висококвалитетних резултата сечења и раном откривању потенцијалних проблема. |

Побољшање квалитета сечења
Побољшање квалитета сечења захтева свеобухватан приступ који узима у обзир параметре процеса, избор опреме и материјала, контролу процеса и инспекцију. Континуираним усавршавањем технологија сечења и оптимизацијом метода процеса, прецизност и стабилност сечења плочица могу се додатно побољшати, пружајући поузданију техничку подршку за индустрију производње полупроводника.
#03 Руковање и испитивање након сечења
3.1 Чишћење и сушење
Кораци чишћења и сушења након сечења плочице су кључни за обезбеђивање квалитета чипа и несметан ток наредних процеса. Током ове фазе, неопходно је темељно уклонити остатке силицијума, остатке расхладне течности и друге загађиваче настале током сечења. Подједнако је важно осигурати да се чипови не оштете током процеса чишћења, а након сушења осигурати да на површини чипа не остане влаге како би се спречили проблеми попут корозије или електростатичког пражњења.
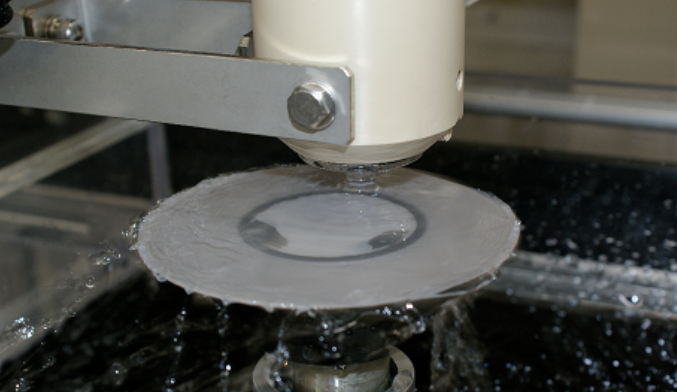
Руковање након сечења: Процес чишћења и сушења
Корак процеса | Садржај | Утицај |
Процес чишћења | -МетодКористите специјализована средства за чишћење и чисту воду, у комбинацији са ултразвучним или механичким техникама четкања за чишћење. | Обезбеђује темељно уклањање загађивача и спречава оштећење чипова током чишћења. |
-Избор средства за чишћењеИзаберите на основу материјала плочице и врсте загађивача како бисте осигурали ефикасно чишћење без оштећења чипа. | Прави избор средства је кључан за ефикасно чишћење и заштиту од струготине. | |
-Контрола параметараСтрого контролишите температуру, време и концентрацију раствора за чишћење како бисте спречили проблеме са квалитетом изазване неправилним чишћењем. | Контроле помажу да се избегне оштећење плочице или остављање загађивача, обезбеђујући конзистентан квалитет. | |
Процес сушења | -Традиционалне методеПриродно сушење ваздухом и сушење топлим ваздухом, која имају ниску ефикасност и могу довести до накупљања статичког електрицитета. | Може довести до споријег времена сушења и потенцијалних проблема са статичким електрицитетом. |
-Модерне технологијеКористите напредне технологије као што су вакуумско сушење и инфрацрвено сушење како бисте осигурали да се чипови брзо осуше и избегли штетне ефекте. | Бржи и ефикаснији процес сушења, смањујући ризик од статичког пражњења или проблема повезаних са влагом. | |
Избор и одржавање опреме | -Избор опремеВисоко ефикасне машине за чишћење и сушење побољшавају ефикасност обраде и фино контролишу потенцијалне проблеме током руковања. | Висококвалитетне машине обезбеђују бољу обраду и смањују вероватноћу грешака током чишћења и сушења. |
-Одржавање опремеРедовна инспекција и одржавање опреме осигуравају да она остане у оптималном радном стању, гарантујући квалитет чипова. | Правилно одржавање спречава кварове опреме, обезбеђујући поуздану и висококвалитетну обраду. |
Чишћење и сушење након сечења
Кораци чишћења и сушења након сечења плочице су сложени и деликатни процеси који захтевају пажљиво разматрање више фактора како би се осигурао коначни исход обраде. Коришћењем научних метода и ригорозних процедура, могуће је осигурати да сваки чип улази у наредне фазе паковања и тестирања у оптималном стању.
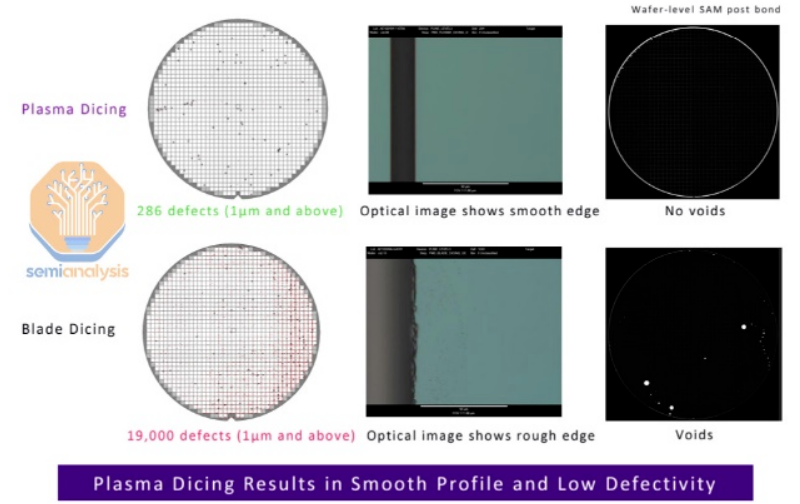
Инспекција и испитивање након сечења
Корак | Садржај | Утицај |
Корак инспекције | 1.Визуелни прегледКористите визуелну или аутоматизовану опрему за инспекцију да бисте проверили видљиве недостатке попут пукотина, крхотина или контаминације на површини чипа. Брзо идентификујте физички оштећене чипове како бисте избегли отпад. | Помаже у идентификовању и елиминисању неисправних струготина у раној фази процеса, смањујући губитак материјала. |
2.Мерење величинеКористите прецизне мерне уређаје за прецизно мерење димензија чипа, осигуравајући да величина реза испуњава спецификације дизајна и спречавајући проблеме са перформансама или потешкоће са паковањем. | Обезбеђује да су чипови унутар потребних ограничења величине, спречавајући деградацију перформанси или проблеме са склапањем. | |
3.Тестирање електричних перформансиПроцените кључне електричне параметре као што су отпор, капацитет и индуктивност, како бисте идентификовали неусаглашене чипове и осигурали да само чипови квалификовани за перформансе пређу у следећу фазу. | Обезбеђује да се само функционални и чипови тестирани на перформансе користе у процесу, смањујући ризик од квара у каснијим фазама. | |
Корак тестирања | 1.Функционално тестирањеПроверити да ли основна функционалност чипа ради како је предвиђено, идентификовати и елиминисати чипове са функционалним абнормалностима. | Осигурава да чипови испуњавају основне оперативне захтеве пре него што пређу на касније фазе. |
2.Тестирање поузданостиПроцените стабилност перформанси чипа при дужем коришћењу или у тешким условима, што обично укључује старење на високим температурама, тестирање на ниским температурама и тестирање влажности како би се симулирали екстремни услови у стварном свету. | Обезбеђује да чипови могу поуздано да функционишу у различитим условима околине, побољшавајући дуговечност и стабилност производа. | |
3.Тестирање компатибилностиПроверите да ли чип исправно ради са другим компонентама или системима, осигуравајући да нема кварова или погоршања перформанси због некомпатибилности. | Обезбеђује несметан рад у стварним апликацијама спречавањем проблема са компатибилношћу. |
3.3 Паковање и складиштење
Након сечења плочице, чипови су кључни резултат процеса производње полупроводника, а фазе њиховог паковања и складиштења су подједнако важне. Правилне мере паковања и складиштења су неопходне не само за обезбеђивање безбедности и стабилности чипова током транспорта и складиштења, већ и за пружање снажне подршке за наредне фазе производње, тестирања и паковања.
Резиме фаза инспекције и испитивања:
Кораци инспекције и тестирања чипова након сечења плочице обухватају низ аспеката, укључујући визуелни преглед, мерење величине, тестирање електричних перформанси, функционално тестирање, тестирање поузданости и тестирање компатибилности. Ови кораци су међусобно повезани и допуњују се, формирајући чврсту баријеру за осигурање квалитета и поузданости производа. Строгим поступцима инспекције и тестирања, потенцијални проблеми се могу идентификовати и брзо решити, осигуравајући да коначни производ испуњава захтеве и очекивања купаца.
Аспект | Садржај |
Мере паковања | 1.АнтистатичкоМатеријали за паковање треба да имају одлична антистатичка својства како би се спречило да статички електрицитет оштети уређаје или утиче на њихове перформансе. |
2.Отпоран на влагуМатеријали за паковање треба да имају добру отпорност на влагу како би се спречила корозија и погоршање електричних перформанси изазвано влагом. | |
3.Отпоран на ударцеМатеријали за паковање треба да обезбеде ефикасну апсорпцију удара како би заштитили чипове од вибрација и удара током транспорта. | |
Окружење за складиштење | 1.Контрола влажностиСтрого контролишите влажност у одговарајућем опсегу како бисте спречили апсорпцију влаге и корозију узроковану прекомерном влажношћу или статичким проблемима узрокованим ниском влажношћу. |
2.ЧистоћаОдржавајте чисто окружење за складиштење како бисте избегли контаминацију сечке прашином и нечистоћама. | |
3.Контрола температуреПодесите разуман температурни опсег и одржавајте стабилност температуре како бисте спречили убрзано старење услед прекомерне топлоте или проблема са кондензацијом изазваних ниским температурама. | |
Редовна инспекција | Редовно прегледајте и процењујте ускладиштене чипове, користећи визуелне прегледе, мерења величине и тестове електричних перформанси како бисте благовремено идентификовали и решили потенцијалне проблеме. На основу времена и услова складиштења, планирајте употребу чипова како бисте осигурали да се користе у оптималном стању. |
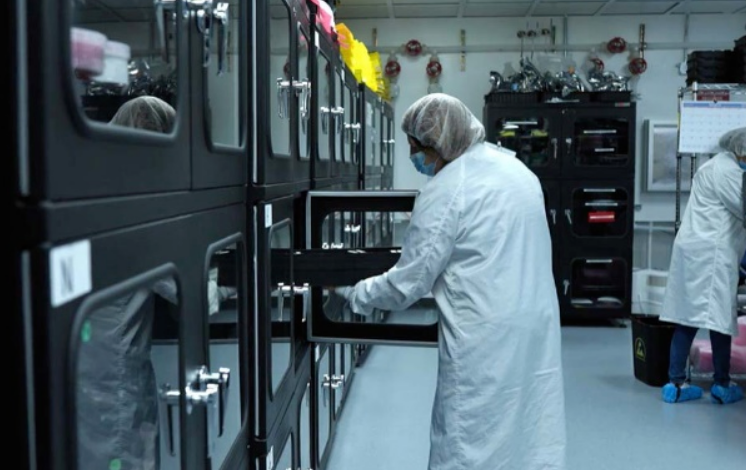
Проблем микропукотина и оштећења током процеса сечења плочице представља значајан изазов у производњи полупроводника. Напрезање резањем је главни узрок овог феномена, јер ствара ситне пукотине и оштећења на површини плочице, што доводи до повећања трошкова производње и смањења квалитета производа.
Да би се решио овај изазов, кључно је минимизирати напрезање резања и применити оптимизоване технике сечења, алате и услове. Пажљива пажња посвећена факторима као што су материјал сечива, брзина сечења, притисак и методе хлађења може помоћи у смањењу стварања микропукотина и побољшању укупног приноса процеса. Поред тога, текућа истраживања напреднијих технологија сечења, као што је ласерско сечење, истражују начине за даље ублажавање ових проблема.
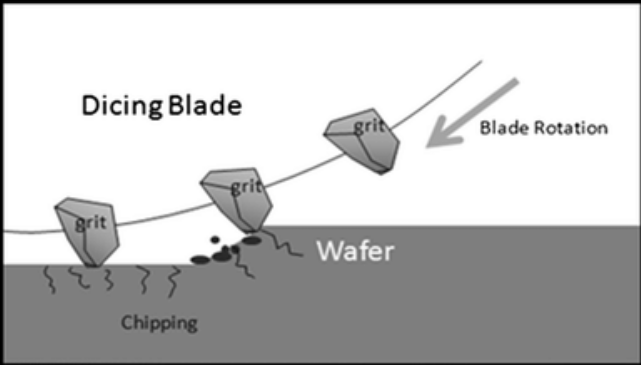
Као крхки материјал, плочице су склоне унутрашњим структурним променама када су изложене механичком, термичком или хемијском напрезању, што доводи до стварања микропукотина. Иако ове пукотине можда нису одмах приметне, оне се могу проширити и изазвати озбиљнија оштећења како производни процес напредује. Овај проблем постаје посебно проблематичан током наредних фаза паковања и тестирања, где температурне флуктуације и додатна механичка напрезања могу проузроковати да се ове микропукотине развију у видљиве преломе, што потенцијално може довести до квара чипа.
Да би се ублажио овај ризик, неопходно је пажљиво контролисати процес сечења оптимизацијом параметара као што су брзина сечења, притисак и температура. Коришћење мање агресивних метода сечења, као што је ласерско сечење, може смањити механичко напрезање на плочици и минимизирати стварање микропукотина. Поред тога, примена напредних метода инспекције попут инфрацрвеног скенирања или рендгенског снимања током процеса сечења плочице може помоћи у откривању ових пукотина у раној фази пре него што изазову даљу штету.
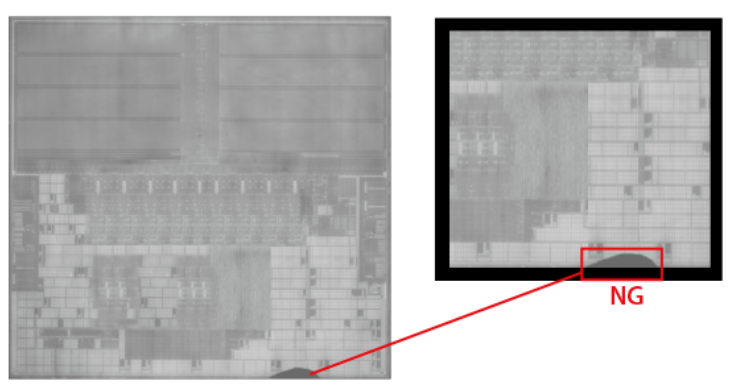
Оштећење површине плочице је значајан проблем у процесу сечења, јер може директно утицати на перформансе и поузданост чипа. Таква оштећења могу бити узрокована неправилном употребом алата за сечење, нетачним параметрима сечења или материјалним дефектима самог плочице. Без обзира на узрок, ова оштећења могу довести до промена електричног отпора или капацитета кола, што утиче на укупне перформансе.
Да би се решили ови проблеми, истражују се две кључне стратегије:
1. Оптимизација алата за резање и параметараКоришћењем оштријих сечива, подешавањем брзине сечења и модификовањем дубине сечења, концентрација напрезања током процеса сечења може се минимизирати, чиме се смањује могућност оштећења.
2. Истраживање нових технологија сечењаНапредне технике попут ласерског сечења и плазма сечења нуде побољшану прецизност, а истовремено потенцијално смањују ниво оштећења нанете плочици. Ове технологије се проучавају како би се пронашли начини за постизање високе тачности сечења уз минимизирање термичког и механичког напрезања на плочици.
Подручје термичког удара и његов утицај на перформансе
У процесима термичког сечења, као што су ласерско и плазма сечење, високе температуре неизбежно стварају зону термичког удара на површини плочице. Ова област, где је температурни градијент значајан, може променити својства материјала, утичући на коначне перформансе чипа.
Утицај зоне термичког утицаја (TAZ):
Промене кристалне структуреПод високим температурама, атоми унутар материјала плочице могу се преуредити, што узрокује изобличења у кристалној структури. Ово изобличење слаби материјал, смањујући његову механичку чврстоћу и стабилност, што повећава ризик од квара чипа током употребе.
Промене електричних својставаВисоке температуре могу променити концентрацију и мобилност носилаца набоја у полупроводничким материјалима, утичући на електричну проводљивост чипа и ефикасност преноса струје. Ове промене могу довести до пада перформанси чипа, што га потенцијално чини неприкладним за његову намену.
Да би се ублажили ови ефекти, контрола температуре током сечења, оптимизација параметара сечења и истраживање метода попут млазева хлађења или третмана накнадне обраде су неопходне стратегије за смањење обима термичког утицаја и одржавање интегритета материјала.
Генерално, и микропукотине и зоне термичког удара представљају кључне изазове у технологији сечења плочица. Континуирано истраживање, уз технолошки напредак и мере контроле квалитета, биће неопходно како би се побољшао квалитет полупроводничких производа и повећала њихова конкурентност на тржишту.
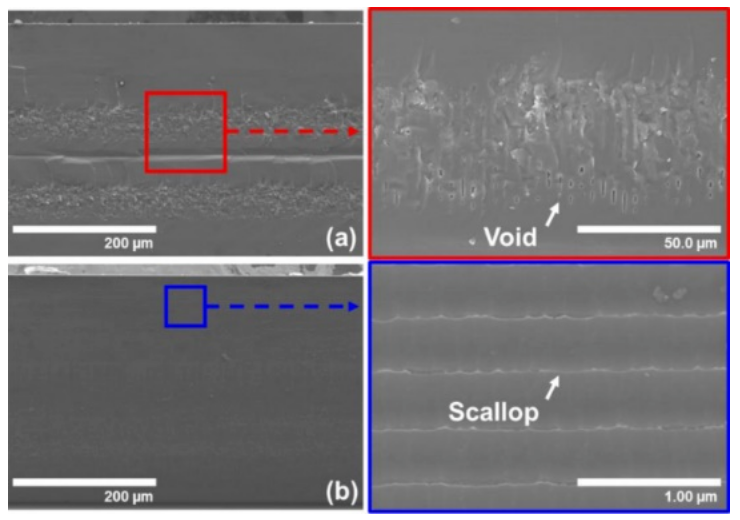
Мере за контролу зоне термичког утицаја:
Оптимизација параметара процеса резањаСмањење брзине и снаге сечења може ефикасно минимизирати величину зоне термичког удара (TAZ). Ово помаже у контроли количине топлоте генерисане током процеса сечења, што директно утиче на својства материјала плочице.
Напредне технологије хлађењаПримена технологија попут хлађења течним азотом и микрофлуидног хлађења може значајно ограничити опсег зоне термичког удара. Ове методе хлађења помажу у ефикаснијем расипању топлоте, чиме се чувају својства материјала плочице и минимизирају термичка оштећења.
Избор материјалаИстраживачи истражују нове материјале, као што су угљеничне наноцеви и графен, који поседују одличну топлотну проводљивост и механичку чврстоћу. Ови материјали могу смањити зону термичког удара, а истовремено побољшати укупне перформансе чипова.
Укратко, иако је зона термичког удара неизбежна последица технологија термичког сечења, она се може ефикасно контролисати оптимизованим техникама обраде и избором материјала. Будућа истраживања ће се вероватно фокусирати на фино подешавање и аутоматизацију процеса термичког сечења како би се постигло ефикасније и прецизније сечење вафла.

Стратегија баланса:
Постизање оптималне равнотеже између приноса вафла и ефикасности производње је стални изазов у технологији сечења вафла. Произвођачи морају да узму у обзир више фактора, као што су потражња на тржишту, трошкови производње и квалитет производа, како би развили рационалну стратегију производње и параметре процеса. Истовремено, увођење напредне опреме за сечење, побољшање вештина оператера и побољшање контроле квалитета сировина су неопходни за одржавање или чак побољшање приноса уз повећање ефикасности производње.
Будући изазови и могућности:
Са напретком технологије полупроводника, сечење плочица се суочава са новим изазовима и могућностима. Како се величине чипова смањују, а интеграција повећава, захтеви за прецизношћу и квалитетом сечења значајно расту. Истовремено, нове технологије пружају нове идеје за развој техника сечења плочица. Произвођачи морају да прате динамику тржишта и технолошке трендове, континуирано прилагођавајући и оптимизујући производне стратегије и параметре процеса како би задовољили промене на тржишту и технолошке захтеве.
Закључно, интегрисањем разматрања тржишне потражње, трошкова производње и квалитета производа, као и увођењем напредне опреме и технологије, унапређењем вештина оператера и јачањем контроле сировина, произвођачи могу постићи најбољу равнотежу између приноса плочице и ефикасности производње током сечења плочице, што доводи до ефикасне и висококвалитетне производње полупроводничких производа.
Будући изгледи:
Са брзим технолошким напретком, технологија полупроводника напредује невиђеном брзином. Као кључни корак у производњи полупроводника, технологија сечења плочица је спремна за узбудљиве нове развоје. Гледајући у будућност, очекује се да ће технологија сечења плочица постићи значајна побољшања у прецизности, ефикасности и трошковима, уносећи нову виталност у континуирани раст индустрије полупроводника.
Повећање прецизности:
У тежњи ка већој прецизности, технологија сечења плочица ће континуирано померати границе постојећих процеса. Дубинским проучавањем физичких и хемијских механизама процеса сечења и прецизном контролом параметара сечења, постићи ће се финији резултати сечења како би се задовољили све сложенији захтеви дизајна кола. Поред тога, истраживање нових материјала и метода сечења значајно ће побољшати принос и квалитет.
Повећање ефикасности:
Нова опрема за сечење плочица фокусираће се на паметан и аутоматизован дизајн. Увођење напредних система управљања и алгоритама омогућиће опреми да аутоматски подешава параметре сечења како би се прилагодила различитим материјалима и захтевима дизајна, чиме се значајно побољшава ефикасност производње. Иновације попут технологије сечења више плочица и система за брзу замену сечива играће кључну улогу у повећању ефикасности.
Смањење трошкова:
Смањење трошкова је кључни правац за развој технологије сечења плочица. Како се развијају нови материјали и методе сечења, очекује се да ће трошкови опреме и одржавања бити ефикасно контролисани. Поред тога, оптимизација производних процеса и смањење стопе отпада додатно ће смањити отпад током производње, што ће довести до смањења укупних трошкова производње.
Паметна производња и Интернет ствари:
Интеграција паметне производње и технологија Интернета ствари (IoT) донеће трансформативне промене у технологију сечења плочица. Кроз међусобну повезаност и дељење података између уређаја, сваки корак производног процеса може се пратити и оптимизовати у реалном времену. Ово не само да побољшава ефикасност производње и квалитет производа, већ компанијама пружа и прецизније прогнозе тржишта и подршку у доношењу одлука.
У будућности, технологија сечења плочица ће донети изузетан напредак у прецизности, ефикасности и трошковима. Ови напредци ће покренути континуирани развој полупроводничке индустрије и донети више технолошких иновација и погодности људском друштву.
Време објаве: 19. новембар 2024.